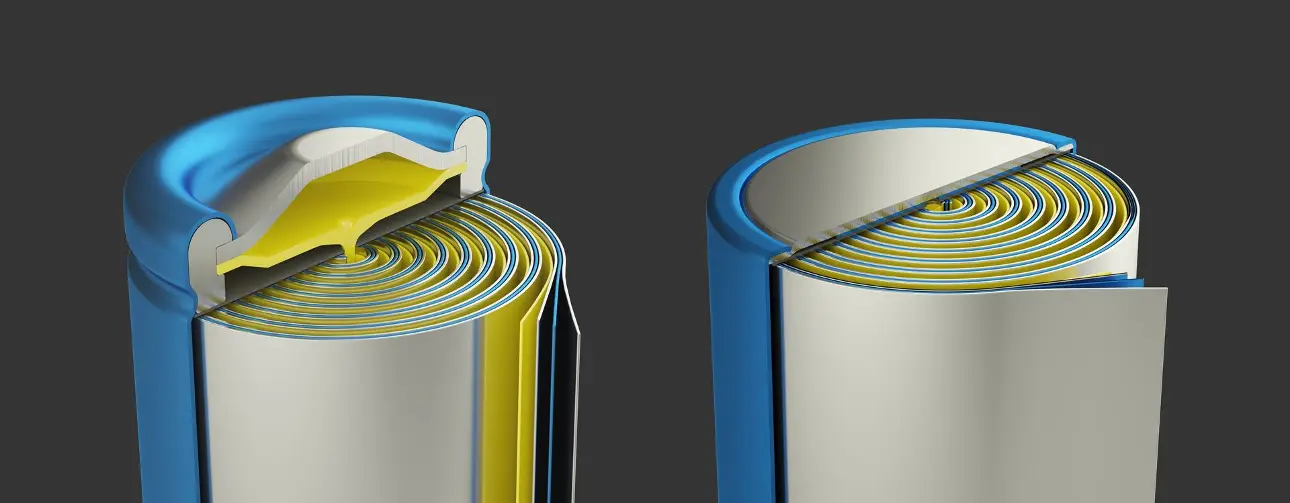
Building a DFMEA for a battery cell is a complex task given the complexity of the electro-chemical, mechanical and electrical interfaces, to understand and document the intricate relationships between the failure effects, modes and causes of the battery cell.
Followed automotive VDA/AIAG 2019 FMEA standard.
Relyence FMEA software tool was used.
Full eBOM structure of material, component and assembly failure analysis was conducted.
Creation of boundary, p-diagrams, worksheets & DVP&R items.
Total time 200hrs of workshops, development & implementation
Lets start discussing your battery cell DFMEA needs today.
Contact us
DFMEA Challenges
TJ Digital Systems were approached to build a DFMEA for a high-profile a customer, looking to license new NMC 21700 cylindrical battery cell into the market. Current challenges for the customer were:
"Takes too long & too complicated"
"Dedicated time and people to support, constant scope creep"
“Inconsistent Scoring of Severity, Occurrence and Detection”
“SC & CC definition – constant discussion between departments on FMs FCs & FEs"
“Hard to scope and bound, creeps into process failure modes"
DFMEA Opportunities
"Generic DFMEA that is easy to understand, with links to DVP" - The value was to understand the potential failure effect, modes and causes and how they could be mitigated through simulation or physical testing.
"Relevant control identified not just SCs & CCs" - Fully understand the reasons, with pointer to evidence, behind the Critical and Special Characteristics (CCs & SCs)
"Knowledge is captured, accessed across the business and not lost" - Ensure detailed knowledge and knowhow was captured and document, so it can be share across the wider business.
"Generic DFMEA prepared for components, which can be tailored for customers" - Have a blueprint of foundational knowledge which can be applied across multiple battery cells.
"Risk based mindset in the business" - Establish a risked based mindset to design throughout the technology team and wider business.
DFMEA Future Benefits
"Customer team can lead workshops with customers to manage their product development risk" - This could create an additional value stream for the customer.
"Anticipate potential faults in customer products” - Hidden failure modes in battery cell development can be very costly so early identification is crucial.
"Roll out to the PFMEA" - Customer aims to roll out the same methodology & approach to the battery cell Process FMEA.
"Tool to manage & boost production yields" - Ability to understand potential design failure modes before they are transferred to process & manufacture, to ensure early capture and corrective actions are implemented.
DFMEA Process Steps
DFMEA - Boundary Diagram
The first key step is to visualise the "focus item" during a workshop and collaborative environment, with cross-functional team. The aim is to understand the possible interactions and what type interface could occur, e.g. thermal energy transfer.
TJ Digital System 2024
DFMEA - P-Diagram
The P-Diagram is structured approach to eliciting the inputs, outputs, function, control factors and sensitivities for the "focus item". You must keep review and building the p-diagram as the design matures.
TJ Digital System 2024
DFMEA - Worksheet
The worksheet is where you combine all the information gathered in the Boundary and P-Diagrams, and you start to conduct the failure and risk analysis.
TJ Digital System 2024
Lets start solving your DFMEA challenges today
What are the requirements and challenges facing you in 2024 and beyond?