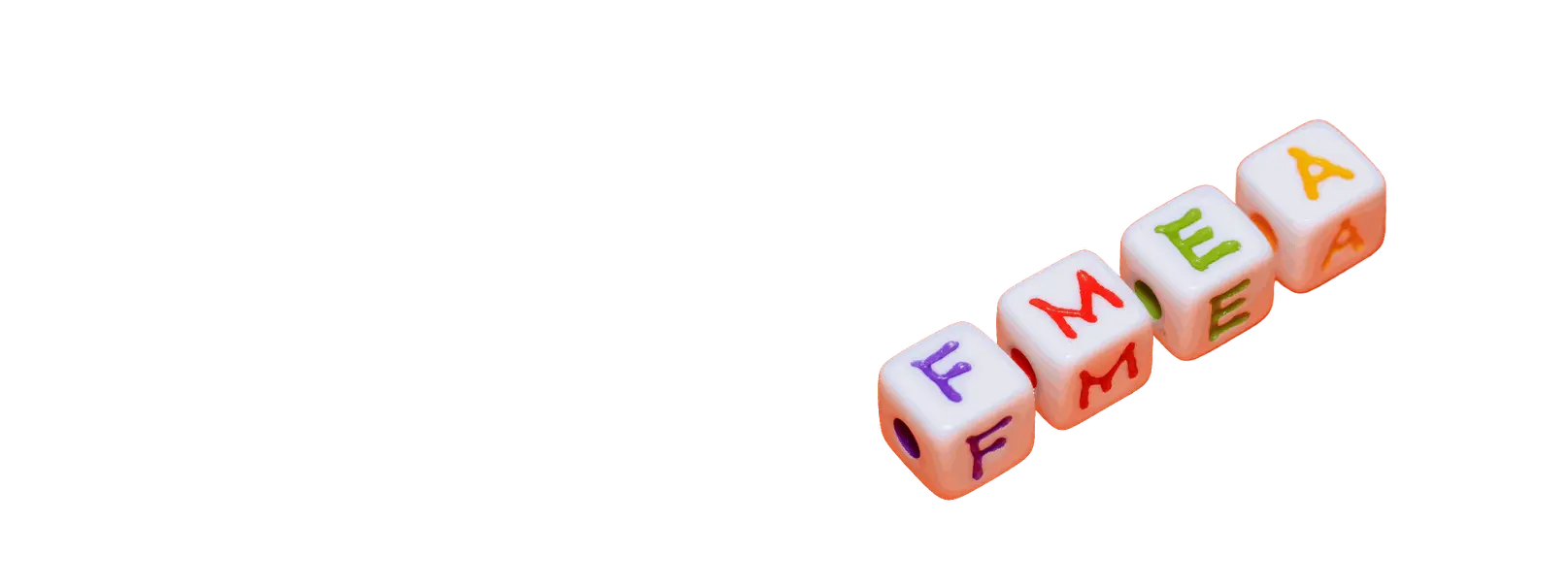
Build a risk based thinking culture within your business with FMEA. We have an excellent understanding of the FMEA methodology, following the AIAG/VDA 2019 standards and using the Relyence FMEA software tool. We offer the following;
Design FMEAs & Design Validation and and Report (DVP&R).
Process FMEAs, Process Flow & Control Plans.
Critical reviews on new or existing products, systems or processes.
FMEA facilitator support and training sessions.
Whether you’re looking to start from starch or want to enhance your knowledge on FMEA we offer flexibility and deliver the results you need.
Lets start discussing your FMEA needs today.
Contact us
What is FMEA?
Failure Mode and Effects Analysis (FMEA) is a methodology that has played a crucial role in ensuring the safety and reliability of complex systems. FMEA is a systematic, structured approach used to identify and evaluate potential failure modes within a system, product, or process.
Analytical technique to systematically assess, during the Design (DFMEA) and or Process (PFMEA) development stages, Failure Modes and their associated Failure Causes have been considered, addressed and then confirmed by validation testing, to reduce the Failure Effects.
It is a Living Record where every related system, subsystem, assembly and component should be evaluated.
FMEA can act as a detailed and documented “storyboard” from a cross functional team, who analyse Failure Mode and Causes, based on experience and knowledge of what could go wrong, to reduce and manage product and or process risk.
Requirement from many OEMs (Automotive, Aerospace etc..) suppliers of critical components or systems where the IP for the system, sub-system or component is owned by the supplier. OEMs will typically audit suppliers to ensure they have follow a structured and "risk" based approach to design and verification.
ISO 9001 : 2015 mandates that a company has a design & verification process and procedures, to ensure their products or services meet the requirements as outlined in ISO 9001 : 2015.
What are the Benefits of FMEA?
Early Risk Identification: FMEA facilitates early identification of potential failures, allowing for proactive risk mitigation and prevention.
Improved Design or Process: By identifying failure mode and their causes, FMEA promotes design or process improvements to enhance system reliability and safety.
Cost Reduction: FMEA helps avoid expensive recalls, or accidents by addressing potential failures during the design and development stages, or with incorrectly specified equipment.
Enhanced Safety Culture: FMEA fosters a safety-conscious culture within businesses, encouraging a systematic approach to risk management.
Battery Cell DFMEA
What are the Limitations of FMEA?
Subjectivity: FMEA involves subjective judgments and ratings, which can introduce variability in the analysis results. This can be mitigated by have appropriate cross-functional knowledge.
Incomplete Analysis: If not conducted thoroughly, FMEA may miss potential failure modes or their effects, compromising the overall effectiveness. This is often attributed to poor quality inputs for FMEA.
Time-Consuming: FMEA can be time-consuming, particularly for complex systems requiring dedicated resources, expertise and defined process methodologies.
Single point failures: FMEA allows for the analysis of risks associated with single point failures.
DFMEA Process Steps
Lets start solving your FMEA challenges today
What are the requirements and challenges facing you in 2024 and beyond?